von Karin Diederich
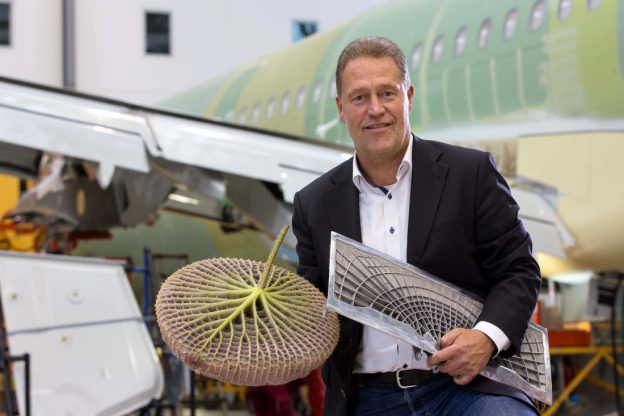
Peter Sander. Quelle: Airbus
Airbus nutzt das Potenzial der additiven Fertigung für Luft- und Raumfahrt
Airbus ist weltweiter Vorreiter im Bereich des 3D-Drucks. Der Luft- und Raumfahrtkonzern hat in Bremen ein Technologiezentrum für die neue Fertigungstechnologie aufgebaut. Einer von vielen Gründen, weshalb die Hansestadt zu einem europäischen 3D-Druck-Hotspot geworden ist. Peter Sander ist 3D-Druck-Experte im Bereich Emerging Technologies & Concepts bei Airbus und gehört zu den Pionieren der industriellen Nutzung in der additiven Fertigung. Er verrät uns wie es dem Großkonzern gelang, die innovative Technologie erfolgreich einzusetzen und wie auch kleine und mittelständische Unternehmen einen Einstieg finden können.Herr Sander, welche Rolle spielt 3D-Druck bei Airbus heute?
Sander: Die Material- und Prozessentwickler bei Airbus in Bremen beschäftigen sich mit der Thematik bereits seit über 15 Jahren, zunächst insbesondere mit dem Fokus auf Kunststoffe. Das Rapid Prototyping* war zu Beginn noch wenig industrialisierbar und hatte daher keinen nennenswerten Stellenwert im Konzern. Dies hat sich in den letzten 5-10 Jahren stark geändert. Inzwischen findet der 3D-Druck konzernweit Anwendung. Alle haben erkannt, dass der 3D-Druck ein enormes Potenzial besitzt.*Schnelle Herstellung von Musterbauteilen/Prototypen mittels 3D-Druck-Techniken
Wie ist es dazu gekommen?
Sander: Bei Airbus haben wir 2010 eine „Innovation-Cell“ gegründet. Dabei handelt es sich um ein interdisziplinäres, selbstorganisiertes Team, welches an den normalen Top-Down Prozessen vorbei agieren konnte und sollte. Es ging darum, Innovationstechniken zu entwickeln, die schnell sind und diese auch praktisch zu demonstrieren Der Fokus lag dabei erst mal auf dem 3D-Druck sowie automatischen Design. Wir suchten Experten, Anwendungsfälle und schrieben konzerninterne Kampagnen aus, um die neuen Fertigungsmöglichkeiten konzernweit bekanntzumachen und voranzubringen. Besonders die Kampagnen haben uns dabei sehr geholfen.Wie tragen diese Kampagnen zum Innovationsprozess bei Airbus bei?
Sander: Kampagnen sind europaweite Ausschreibungen, in diesem Fall Vorschläge für die Anwendung neuer Technologien. Die Effektivste im 3D-Druck war 2014: Wir haben rund 200 Vorschläge in sechs Wochen erhalten. Nach einem Vierteljahr Auswertungs- und Herstellungsphase haben die 13 Finalisten dann der Airbus-Geschäftsführung vorgestellt, was im Bereich 3D-Druck möglich ist. Daraus resultierte der Auftrag, eine europaweite 3D-Druck Plattform aufzubauen, eine industrielle Umsetzungsplattform. Diese ist seit Ende 2014 für Gesamt-Airbus Commercial – also Flugzeuge - in Betrieb.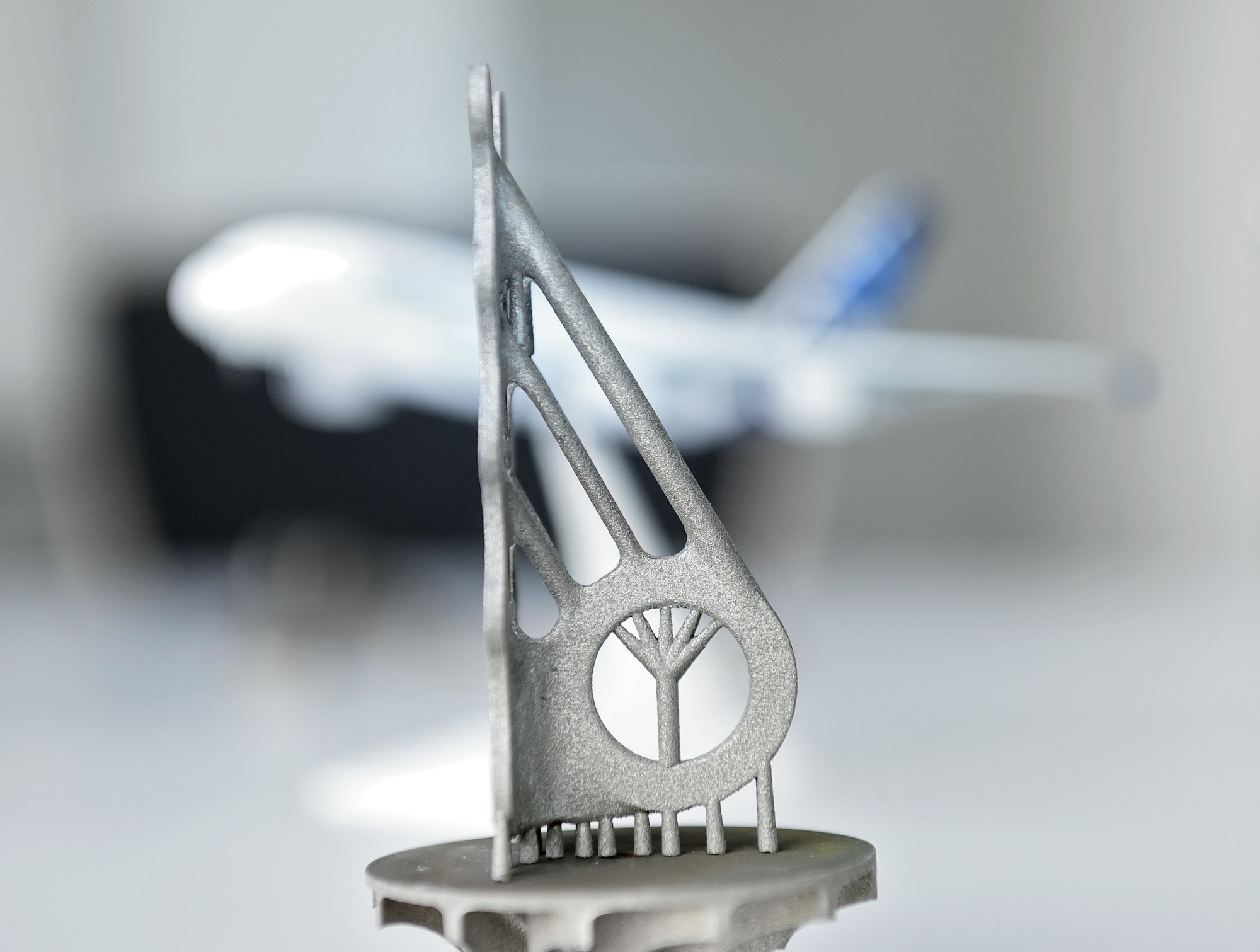
Titanhalter aus dem 3D-Drucker. Bild: WFB
Welche Aufgaben hat die Plattform?
Sander: Sie organisiert die Material- und Prozessentwicklung, entwirft neue Designtools, und schaut sich Anwendungsfälle an. Die europaweite Plattform mit über 40 Mitarbeitern in Deutschland, England, Frankreich, Spanien treibt den 3D-Druck innerhalb des Unternehmens voran. Wir haben im letzten Jahr knapp 10 Millionen Euro investiert, für dieses Jahr ist eine ähnliche Größenordnung angesetzt.Welche Erfolge kann sie denn bisher vorweisen?
Sander: 2014 wurde unser erstes gedrucktes Kunststoff-Ersatzteil an einen Kunden ausgeliefert und es sind die ersten Teile in Testflugzeugen geflogen, beispielsweise ein Titanhalter. Das war wichtig um zu zeigen, dass 3D-Druck in der Luftfahrt funktioniert. Im letzten Jahr haben wir zum Beispiel zusammen mit der Firma Liebherr weltweit erstmalig eine gedruckte hydraulische Flugsteuerungskomponente aus Titan geflogen, deren Gehäuse 55 Prozent leichter ist, als ihre Vorgänger. Sie funktioniert und ist noch an Board unserer eigenen A380 Testmaschine!Angestrebt ist die Serienfertigung derartiger Komponenten ab 2020. Im Prinzip haben wir uns langsam herangetastet, erst mit der seriellen Umsetzung der Halter und uns dann größeren Projekten zugewendet. Inzwischen arbeiten wir hier in Bremen zum Beispiel an der Vorentwicklung hochintegrierter Hydraulikkomponenten.
Außerdem wurden mehrere unserer Projekte hochrangig gewürdigt: Mit dem ersten fliegenden Titanhalter waren wir 2015 im Finale für den Deutschen Zukunftspreis von Bundespräsident Gauck, mit dem Konzept für eine bionische Trennwand bekamen wir den ECO-Design-Award vom Bundesumweltministerium und mit unseren vier Meter gedruckten THOR Flugzeug sind wir sogar im Guinness Buch der Rekorde 2018 als die ersten weltweit, die ein fliegendes Flugzeug gedruckt haben
Wo sehen Sie die Vorteile vom 3D-Druck im Flugzeugbau gegenüber herkömmlichen Verfahren?
Sander: Das zukünftige Anwendungsspektrum ist immens. Statt Lagerung der Ersatzteile zu Hunderten irgendwo im Lager und entsprechender Transporte zum Bestimmungsort, wird zukünftig per Additive Manufacturing (AM) das digitale Ersatzteil on demand und verwendungsnah produziert. Das ist eine riesige Ressourceneinsparung. Ein weiteres großes Feld ist die durch AM ermöglichte Bionische- (Topologie optimierte-) Konstruktion mit erheblichen Gewichtseinsparungen, welche wiederum massiv Ressourcen in der Herstellung aber auch im Betrieb des Produktes sparen. Und drittens werden wir in der Zukunft hochintegrale, multifunktionale AM-Komponenten sehen, die einen „Step-Change“ im Produktdesign ermöglichen. Diese Entwicklungsmöglichkeiten werden dazu führen, dass sich der 3D-Druck durchsetzt.Lassen sich denn alle Produkte nachdrucken?
Sander: Es geht darum, Anwendungsfälle zu finden. Nicht alle Werkstoffe sind druckbar. Es gibt da einen riesigen Entwicklungsbedarf. Wenn ich zum Beispiel über Metalle rede, dann geht es immer um schweißbare Werkstoffe. Bei Airbus sind diverse Aluminiumlegierungen im Einsatz, jede Legierung hat eine bestimmte Eigenschaft und ist gut für etwas, aber nicht jede Legierung ist schweißbar.
Peter Sander vor den Teilen des ersten 3D-gedruckten Flugzeugs. Bild: Airbus
Sander: Dazu eine Geschichte: Für die Satellitentechnik wollten wir Alu-Kühlerplatten drucken. In diesem Bereich hat man es mit extremen Temperaturen zu tun, wichtig ist der Wärmeausgleich. Dafür gab es einen speziellen Werkstoff, der früher als nicht druckbar galt. Gefördert durch das Deutsche Luft- und Raumfahrtzentrum (DLR) haben wir in einem Forschungsprojekt dann zusammen mit dem Fraunhofer IAPT (früher LZN) fünf in Frage kommende Werkstoffe auf Ihre 3D-Druck Tauglichkeit verpulvern lassen und geschaut, ob man die wieder verschweißen kann. Zwei davon haben geklappt - ein Material, obwohl es unter Flugzeuganwendungs-Gesichtspunkten als nicht schweißbar galt!
Bastian Müller (bastian.mueller@wah.bremen.de)
Bild oben: Peter Sander. Quelle: Airbus
Sollten kleine und mittlere Unternehmen (KMU) jetzt in die additive Fertigung einsteigen oder noch warten?
Sander: Auf jeden Fall einsteigen! Für KMU ist es aber wichtig zu schauen, bei welchen Teilen es sich lohnen könnte, in den 3D-Druck zu starten. Vielleicht ein Teil, das schwer lieferbar ist, weil beispielsweise ein Gussteil fehlt? Man kann hochqualifizierte Produkte drucken, aber zu Beginn startet man am ehesten zum Beispiel mit einem kleinen, einfachen Halter, um nachzuweisen, dass es sinnvoll möglich ist. Frei nach dem „Lessons-Learned-Prinzip“.Was raten Sie Unternehmen/KMU, die in den 3D-Druck einsteigen wollen?
Sander: Ich rate dazu, sich zu vernetzen. Mittelständlern fehlt es teilweise an Know-How und einer Übersicht über die Chancen, die mit den neuen Fertigungstechniken verbunden sind. Da können wir im Netzwerk helfen. Denn wir dürfen eins nicht vergessen: Ein key-enabler für das zukünftige Bestehen am Markt, ist die Entwicklungsgeschwindigkeit. Wie bringe ich die Entwicklung schnell von meiner Firma auf die Straße? Den Innovationsaufwand kann ein Unternehmen meistens nicht alleine schaffen – und da hilft es, sich im 3D-Druck zu vernetzen. Und hier haben wir bei der BRE3D Initiative wirklich was zu bieten: Es stehen diverse wissenschaftliche Institute aus der Werkstoff-, und Verfahrenstechnik (IFAM, IWT, ISEMP Faser Institut), aber auch aus der Bionik wie das AWI oder der Lehrstuhl für Bionik von Professorin Antonia B. Kesel, mit der wir schon eine langjährige Zusammenarbeit pflegen, zur Unterstützung zur Verfügung.Wie sieht es mit den Kosten aus?
Sander: Erfahrungsgemäß ist die Hinwendung zum 3D-Druck gar nicht teuer. Wenn man eine Idee hat, geht man zu Experten wie beispielsweise dem Bremer Unternehmen Materialise GmbH und entwickelt mit deren fachmännischer Unterstützung einen ersten Prototyp. Die Investition am Anfang ist gar nicht so hoch. Die Industrialisierung erfolgt erst später. Am Anfang brauchen die Unternehmen auch keine eigenen 3D-Drucker. Der Übergang kann ganz soft laufen. Vielen Dank für das Gespräch! Lesen Sie hier, wie Bremen im Bereich 3D-Druck aufgestellt ist und welche Fördermittel und Netzwerke Unternehmen nutzen können. Für Fragen und Anregungen stehen Ihnen folgende Personen zur Verfügung: Peter Sander (peter.sander@airbus.com)Bastian Müller (bastian.mueller@wah.bremen.de)
Bild oben: Peter Sander. Quelle: Airbus